Marine Panels 101 - Types, Benefits, Pros and Cons
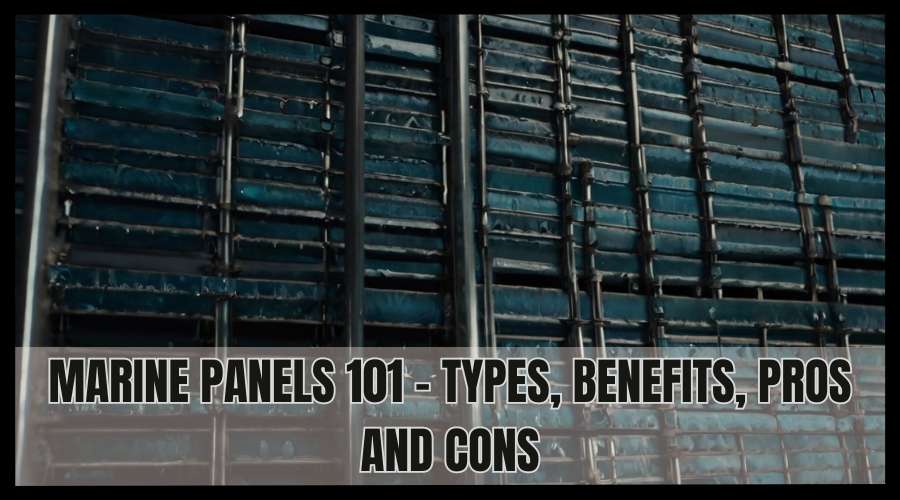
Marine panels play a crucial role in the maritime industry, offering durability, versatility, and performance in a wide range of marine applications. Whether you're involved in boat building, ship repairs, or outfitting a yacht, understanding marine panels' types, benefits, pros, and cons is essential. This comprehensive guide will explore the different types of marine panels available, their advantages, and potential drawbacks to help you make informed decisions.
What Are Marine Panels?
Marine panels are specialized building materials designed to withstand harsh marine environments. They are used in a variety of applications, including boat construction, ship interiors, and coastal architecture. These panels are engineered to resist moisture, rot, and other forms of degradation common in marine settings. Unlike regular wood or composite materials, marine panels are specifically treated or manufactured to endure prolonged exposure to water, salt, and fluctuating weather conditions.
Types of Marine Panels
1. Marine Plywood
Marine plywood is one of the most commonly used marine panels. It is made from high-quality wood veneers that are bonded together using waterproof adhesive. Marine plywood is known for its strength, resistance to moisture, and ability to hold fasteners well. It is available in various grades, with the highest grades offering the best resistance to water and other environmental factors.
2. Aluminum Composite Panels (ACP)
Aluminum Composite Panels are popular for boat builders due to their lightweight and corrosion-resistant properties. These panels consist of two thin layers of aluminum sandwiched around a non-aluminum core, adding rigidity and strength without significant weight. ACPs are also easy to clean and maintain, making them ideal for exterior and interior applications on boats and ships.
3. Fiberglass Reinforced Panels (FRP)
Fiberglass-reinforced Panels (FRP) are another widely used type of marine panel. Made from a combination of fiberglass and resin, these panels are known for their high strength-to-weight ratio and excellent resistance to water and chemicals. FRP panels are often used in vessel areas that require extra durability, such as the hull, deck, and interior walls.
4. PVC Foam Panels
PVC Foam Panels are lightweight, versatile, and resistant to moisture, making them suitable for a variety of marine applications. These panels are often used in interior furnishings, cabinetry, and other non-structural areas where weight is a concern. PVC foam panels are also easy to cut, shape, and install, making them a favorite among DIY boat builders.
5. Honeycomb Core Panels
Honeycomb Core Panels are known for their high strength-to-weight ratio and are often used in constructing high-performance boats and yachts. These panels feature a core made of honeycomb-like structures, usually composed of materials like aluminum, aramid, or polypropylene. The honeycomb design provides exceptional rigidity and impact resistance while keeping the panel lightweight.
6. Thermo-Lite Panels
Thermo-Lite Panels are an innovative type of marine panel made from high-density polyurethane foam reinforced with layers of fiberglass. These panels are highly durable, moisture-resistant, and offer excellent thermal insulation. Thermo-Lite panels are often used when weight reduction is critical, such as in the construction of racing boats and luxury yachts.
7. Coosa Board
Coosa Board is a composite panel made from high-density polyurethane foam and layers of fiberglass. It is known for its strength, durability, and resistance to water, rot, and insects. Coosa Board is often used as a replacement for traditional wood in marine applications, particularly in areas that require structural integrity, such as transoms, decks, and bulkheads.
Benefits of Using Marine Panels
1. Durability
One of the primary benefits of marine panels is their durability. These panels are designed to withstand the harsh conditions of marine environments, including water, salt, and UV radiation exposure. This makes them ideal for boat construction and other marine applications where longevity is essential.
2. Lightweight
Many marine panels, such as aluminum composite panels and PVC foam panels, are lightweight. This is an important factor in boat building, where reducing weight can improve speed, fuel efficiency, and overall performance. Lightweight panels also make installation easier and more manageable.
3. Moisture Resistance
Marine panels are engineered to resist moisture, a critical factor in marine environments. Unlike traditional wood, which can absorb water and rot over time, marine panels are treated or manufactured to repel water and resist decay, ensuring a longer lifespan for your boat or marine structure.
4. Versatility
Marine panels come in a variety of materials and configurations, making them suitable for a wide range of applications. Whether you need panels for structural purposes, interior finishes, or decorative elements, a marine panel meets your needs. This versatility allows boat builders and designers to create customized solutions that meet specific performance and aesthetic requirements.
5. Low Maintenance
Many marine panels, particularly composite material ones, require minimal maintenance. They do not warp, crack, or corrode and can often be cleaned with soap and water. This low maintenance requirement makes them a cost-effective choice in the long run, as they reduce the need for repairs and replacements.
6. Eco-Friendly Options
Some marine panels, such as those made from recycled or sustainable sources, offer an environmentally friendly alternative to traditional building materials. By choosing eco-friendly marine panels, you can reduce your environmental impact while achieving high performance and durability.
Pros and Cons of Marine Panels
1. Pros
· High Strength and Durability: Marine panels are built to withstand the tough conditions of marine environments, providing long-lasting performance.
· Moisture and Rot Resistance: These panels are designed to resist moisture and rot, making them ideal for use in wet and humid conditions.
· Lightweight Construction: Many marine panels are lightweight, making them easy to handle and install while contributing to better vessel performance.
· Versatile Applications: Marine panels can be used in various settings, from structural components to interior furnishings.
· Low Maintenance: The durable and resistant nature of marine panels means they require little upkeep, saving time and money on maintenance.
2. Cons
· Cost: High-quality marine panels, particularly those made from advanced composite materials, can be expensive. This can increase the overall cost of boat building or repairs.
· Specialized Installation: Some marine panels require specialized tools or skills for installation, which may add to the labor cost and complexity of the project.
· Limited Availability: Certain marine panels, especially those with specialized properties, may not be readily available and require special ordering or longer lead times.
· Environmental Impact: While eco-friendly options are available, some marine panels, especially those made from synthetic materials, can have a negative environmental impact.
· Weight Considerations: While many marine panels are lightweight, some options, like marine plywood or honeycomb core panels, can be heavier, which may affect the overall weight of the vessel.
How to Choose the Right Marine Panel
Choosing the right marine panel for your project involves considering several factors, including the intended use, environmental conditions, and budget. Here are some tips to help you make the best choice:
· Determine the Application: Consider where and how the marine panel will be used. Structural applications may require stronger, more durable panels, while interior finishes may prioritize aesthetics and weight.
· Evaluate Environmental Conditions: Consider the specific marine environment your project will be exposed to. Saltwater, humidity, and temperature fluctuations can all impact the performance of marine panels, so choose a material suited to the conditions.
· Consider the Weight: If weight is critical, such as in racing boats or smaller vessels, opt for lightweight materials like aluminum composite panels or PVC foam panels.
· Check for Certifications: Look for marine panels that meet industry standards and certifications, such as Lloyd's Register or the American Bureau of Shipping (ABS). These certifications ensure that the panels meet specific performance and safety criteria.
· Budget Considerations: While high-quality marine panels can be costly, they often provide better durability and longevity, saving money in the long run. Balance your budget with the performance requirements of your project.
· Consult with Experts: If unsure which marine panel is right for your project, consult a marine engineer or a knowledgeable supplier. They can provide valuable insights and recommendations based on your specific needs.
Conclusion
Marine panels are essential in the construction and maintenance of boats, ships, and other marine structures. With various types available, each offering unique benefits and drawbacks, choosing the right marine panel can significantly impact your project's performance, durability, and longevity. By understanding the different options and carefully considering factors like application, environment, and budget, you can select the best marine panel to meet your needs and ensure the success of your marine endeavors.